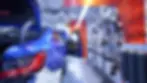
Let's delve deeper into how 36Zero Vision innovative quality inspection system is revolutionizing the manufacturing industry, breaking free from the constraints of traditional methods, and paving the way for a more adaptive, efficient, and precise approach to quality control.
The Inflexibility and Cost of Tradition
Traditional quality inspection systems in manufacturing are characterized by their heavy reliance on specialized hardware and a narrowly focused field of vision. These systems require an array of cameras, each dedicated to inspecting minute sections of a product, such as a specific portion of a car's exterior. This method not only demands perfect environmental conditions—like optimal lighting and precise part placement—but also leads to rigid and expensive setups. Whenever a change occurs in the production line or the design of the manufactured part, the entire quality inspection station struggles to adapt, resulting in increased false positives or missed defects. Furthermore, the reliance on robotic automation, though innovative, introduces its own set of challenges. Any minor alteration in the production process necessitates a complete overhaul of the robot's trajectory and automation planning, rendering the system inflexible and inefficient.
A Software-Driven Leap Forward
Recognizing the limitations and inefficiencies of the existing systems, our team, primarily composed of software engineers without specialized hardware expertise, embarked on a mission in 2019 to revolutionize the quality inspection process. We developed a prototype that leveraged the smartphone as a powerful inspection tool, capitalizing on its large field of view and high-resolution camera capabilities. This approach marked a significant departure from traditional methods, offering a flexible and cost-effective solution for comprehensive quality inspection. Later we also added support for industrial hardware, as it was much easier usecase for us to adopt it, rather than the other way around.
The Core of Innovation: AI and Automation
At the heart of our system lies an advanced AI algorithm and an innovative automation engine. Unlike traditional systems that depend on rigid, rule-based analysis or shallow deep learning models, our algorithm is designed to dynamically adapt to changes in environmental conditions and part designs. It can identify specific defect patterns across a broad field of view, ensuring precise and reliable defect detection without the need for perfect conditions or static part placement.
Our automation engine facilitates the capture of images across the entire part without the constraints of hardware triggers. This flexibility allows the system to subdivide a part's image into smaller segments or "virtual cameras," each capable of conducting detailed inspections on their assigned section. Through our patented technology, we ensure that these subdivided images retain their high resolution and sharpness, enabling our AI to perform accurate inspections on a granular level.
Multi-Stage Deep Learning Model
Our system employs a sophisticated four-stage deep learning process. The first stage involves capturing a sharp, high-resolution image of the part in motion, ensuring a comprehensive field of view. Following this, the image is subdivided into smaller segments without sacrificing quality, thanks to our patented technology. Each segment then undergoes a specific inspection workflow—detecting scratches, assessing conformity, performing metrology checks, and more—powered by our pattern-matching algorithm. The final stage amalgamates the results from each segment, providing a detailed and accurate overall verdict on the part's quality.
The Impact and Future
This innovative approach to quality inspection has proven to be a game-changer in the manufacturing industry. Not only does it significantly reduce the incidence of false positives and undetected faults, but it also offers unparalleled adaptability to changes in production lines and part designs. The system's precision and efficiency have garnered praise from leading OEMs and suppliers, demonstrating its potential to transform quality control processes across the manufacturing sector.
Looking ahead, this technology paves the way for a new era of manufacturing, where quality inspection is no longer a bottleneck but a seamless, integrated process. By embracing software-driven solutions and the power of AI, manufacturers can achieve higher levels of precision and efficiency, driving innovation and maintaining competitiveness in a rapidly evolving industry.